“How am I going to rebuild that rotary tablet press turret?” You’ve probably never had to ask that question before. Modern turrets are designed in multiple pieces, and broken parts can simply be replaced. Advancements in materials, technology, and replacement methods have brought these machines to a point where their outputs are nothing short of amazing. From hand turned table top designs to machines that have output potential of over a million tablets per hour, the tablet press turret continues to innovate. It hasn’t always been so easy, though. Here’s a look at how things have changed in the last several decades.
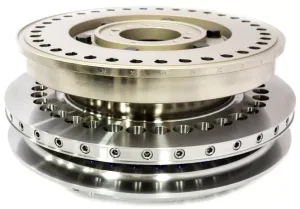
Early Designs
The tablet press design dates back to the early 20th century. Many turrets were originally manufactured in one piece. The material of choice for these early designs was cast iron, which offered the best machinability and wear characteristics at the time. However, when the machines began showing signs of wear, choices were limited and potentially expensive depending on the type of problem. For example, if a single punch bore was wearing out, a bushing could be inserted in its place. But if the die table began showing cracks in the die sockets, there was no simple solution. Many times this meant replacing the turret, which came at heavy cost. The introduction of the multiple piece turret design solved this issue. Upper or lower punch sections, die tables, and driving gears could all be individually replaced.
Die Table Innovations
For die tables, this meant using steel or stainless steel instead of cast iron. This includes the use of chrome for die tables and hardened steel plates to mount on top of die tables. These innovations allow the surface of the die table to withstand much more abrasive products. What exactly is it about steel that suits die tables so well? It all comes down to die table design. A die table has vertical holes for die sockets and horizontal holes for die locks. Because of these crisscrossing holes, there are points in die tables that are much thinner and weaker than others. These are common points of wear when using cast iron.
Since steel has a much greater structural integrity than cast iron, it is far more desirable for die tables. In fact, steel is so much stronger that the risk of cracks appearing between die sockets is almost eliminated.
Turret Construction
It’s a different story for the upper and lower sections of turrets. The punch bores in these sections actually perform better with cast iron. A high tensile strength ductile iron lends itself well to a burnished finish on the punch bores. With cast iron, a roller burnishing tool can flatten out the tool marks from machined holes. This finish (around 8 microns) helps reduce the friction between the punch and bore, giving bores a longer life when maintained well. While a definitive best choice of cast iron grade for punch bores is up for debate, companies experienced with the tablet press turret can offer the best options.
Consulting with a Professional Manufacturer
It’s a different story for the upper and lower sections of turrets. The punch bores in these sections actually perform better with cast iron. A high tensile strength ductile iron lends itself well to a burnished finish on the punch bores. With cast iron, a roller burnishing tool can flatten out the tool marks from machined holes. This finish (around 8 microns) helps reduce the friction between the punch and bore, giving bores a longer life when maintained well. While a definitive best choice of cast iron grade for punch bores is up for debate, companies experienced with the tablet press turret can offer the best options.
Meet the Experts

Andy Lapinsky
Andy Lapinsky has been working for Elizabeth Carbide since 1989, taking on roles of increasing responsibility over the years. Today, he is the manager of engineering and CNC programming where he oversees the design of compression tooling and technical services for Elizabeth tooling customers.

Jim Calvin
Jim Calvin joined Elizabeth in the 1980s making tooling. Early in his career, Jim transitioned to Elizabeth-Hata International (press division) designing and building press control systems, working as a service technician and service manager, servicing and installing equipment, validating, troubleshooting and training. Today, he is General Manager of Elizabeth-Hata International.